Our products have been specifically designed to support the principles of a circular economy. The process of 3D printing allows us to manufacture our luminaire components on demand resulting in zero waste and enables unconstrained design innovation. Furthermore, it enables us to manufacture and assemble in the UK helping to lower the carbon footprint.
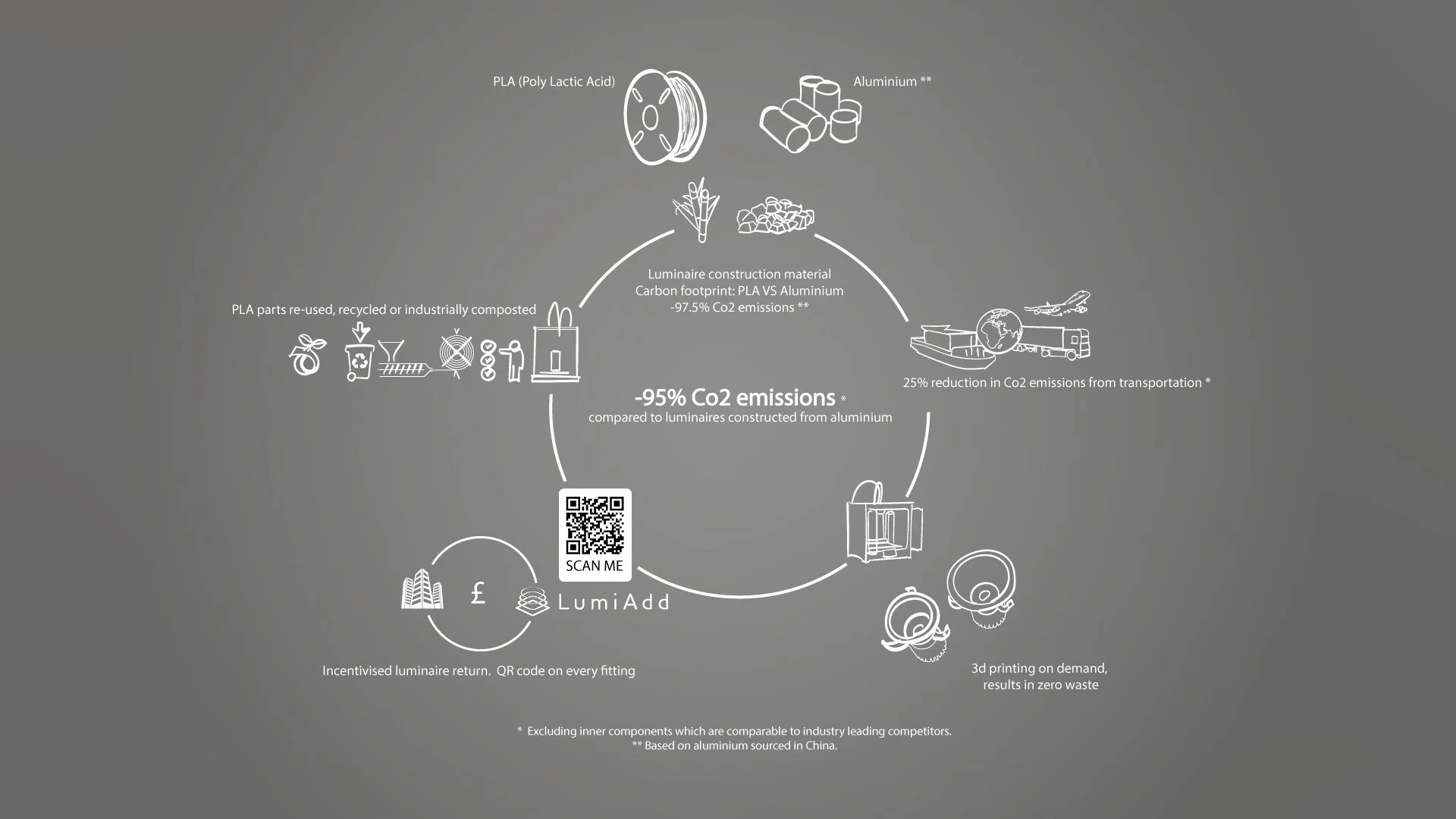
To truly support a circular economy, it is not simply a change in material choice or reducing our carbon footprint. The products life cycle loop needs to be closed which is currently not achieved in the lighting industry. Our luminaires need to be re-used, repaired or re-manufactured with recycling/industrial composting being the last option. It is for this reason that Lumiadd is offering a buy back scheme to support the return of LumiAdd luminaires at the end of their first use to ensure they can be re-used again. All products will have an easily accessible QR code to provide quick and easy access to relevant information on this scheme.
LumiAdd products Rated ‘EXCELLENT CIRCULARITY’ the highest TM66 assessment category
CIBSE TM66: 2021
The Chartered Institution of Building Services Engineers (CIBSE) and the Society of Light and Lighting (SLL) have launched a brand-new Technical Memorandum seeking to identify the extent of current knowledge and provide a framework for action and assessment for all within the lighting industry.
Alongside TM66 they have provided the Circular Economy Assessment Method (CEAM) to give information to all, enable supply push by creating a ‘nuts and bolts’ tool for manufacturers, and to stimulate demand by giving specifiers and clients the questions they need to ask.
Our 3D printed luminaires score very highly using this assessment measure. Our products are in the highest category rated ‘EXCELLENT CIRCULARITY’
We are happy to share our assessment and provide evidence to substantiate the rating on request.
We are using PLA & PLA/PHA bio plastics:
Made from renewable resources corn starch, cassava roots, or sugarcane
Biodegradeable, Compostable*
Production of PLA saves two thirds of the energy needed to make traditional plastics
Carbon dioxide is consumed during the growth of corn, the net greenhouse gas emission of the overall PLA production process can even be considered neutral
Scientifically established that during the biodegradation of PLA bioplastics, there is no net increase in carbon dioxide gas
Can be recycled
RAL colours available
*PLA is compostable in industrial composting conditions. If returned PLA products cannot be re-used or recycled, Lumiadd is committed to composting it.
PHA does not need industrial composting conditions, If returned PHA products cannot be re-used or recycled, Lumiadd is committed to composting it.
Carbon footprint: PLA VS Aluminium
We have designed our luminaires to not only support the principles of a circular economy but considerable design and development has been undertaken to ensure that they are industry leading with regards to performance. Many luminaires available on the market at this level have bodies constructed from die cast aluminium. By replacing the aluminium with bio-based plastics, many of the key components that make up the Lumiadd luminaires have a reduced carbon footprint. This reduction in the materials carbon footprint is illustrated in the graph below where we compare PLA against aluminium sourced in both the Far East and the EU.
Although a high proportion of cast aluminium parts for luminaires are produced in the Far East, the current industry shift to localised production of parts means that it is also relevant to consider the KgCo2 eq/ton figures for the EU in addition to the Far East. As illustrated in the graphs, producing 1 ton of aluminium in the Far East releases 20,000kg of Co2 into the atmosphere. This high figure is a result of the continued use of coal fired power stations. In comparison, EU aluminium produces significantly less Co2, but it is still considerably higher than Co2 emissions attributed to PLA.
Carbon footprint: Weight & Transportation
In addition to the considerable difference in carbon footprint when comparing the production of aluminium and PLA, the difference in material mass provides further reductions in carbon when transporting finished goods in accounted for.
Taking our track mounted spotlight for example, when benchmarking an equivalent luminaire from a leading manufacturer constructed primarily of aluminium, our fitting is 25% lighter due to the use of PLA. The resultant weight difference leads to significant reductions in Co2 emissions coming from transportation.